Why Millimetres Matter with Roof Sealant Applications
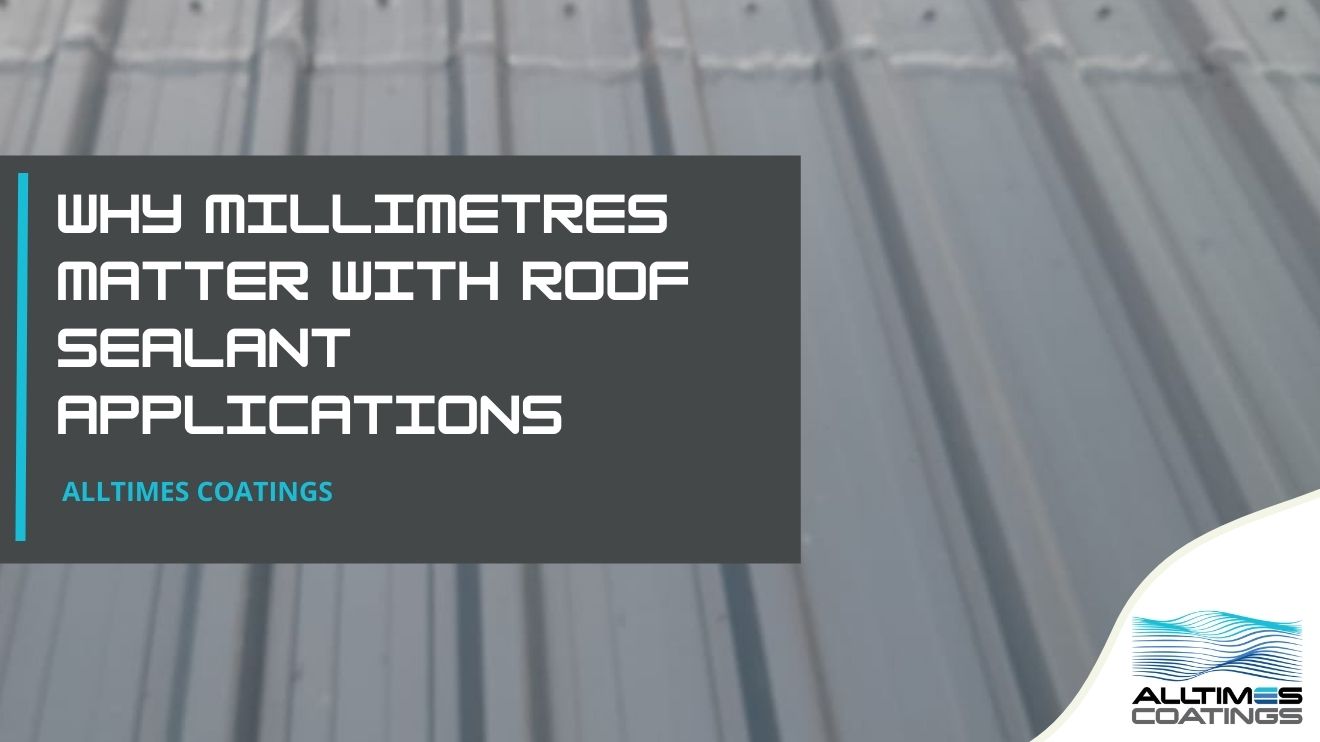
...And Why We Should Take Our Hats off to the Contractors
When working with a new company, I find it useful to speak to the guys responsible for applying the product, talk them through how it’s done and answer any questions they might have, ideally on site.
It was whilst I was preparing for one of these training sessions – which I was due to deliver to a group of new contractors – that a thought came to me,
“How do they budget for material costs, and in particular, the sealant/mastic that is used to seal over-laps on steel roofs…?”
… As allowing for sufficient material and using the correct amount of sealant is critical to keeping a job within budget. And, of course, application rate is dependent on the guys actually doing it!
The Guys Doing the “Grunt” Are Critical
Contractors are instrumental in making sure a job is done on-time, on budget and to a high standard.
And the mastic/sealant example – as mentioned in the introduction – is a perfect way to demonstrate this.
When budgeting, we suggest that they will get 3 linear metres from each cartridge of sealant. This is based on a 10mm bead and the overlap being fairly tight.
However, 1mm difference in the bead size can make a considerable disparity to how much is ordered. Here’s an example:
A 9mm bead will give 3.8 metres from one 310ml cartridge but a 9mm will be only 2.56 linear metres…
…Bearing in mind that some of these jobs can be many thousands of linear metres, 1mm of bead size can be an expensive mistake.
How Can Millimetres Affect Large Projects?
What the Applicators Need to Get Right and Who it Might Affect
To drive this home even further, here are some additional considerations for the contractor in ensuring a top-quality outcome.
Cleaning
If the substrates surface is not cleaned properly before coating, there is a chance of either contamination affecting a coating or adhesion failing.
If it is evident before the job is finished and everyone leaves the site for good, there will be remediation work to be done.
If adhesion fails early and it is apparent that the surface was not cleaned properly, any warranty will become invalid.
Cut-Edge-Corrosion Preparation
There have been some shocking examples of work here, and diligence and attention to detail is paramount.
First off, the loose rust and powder needs removing, followed by a feathering of the edge of the peeling plastisol or other coating.
We insist on an anti-corrosion primer on any tight rust and bare steel if the galvanized coating has gone. Not all companies specify the primer and we do not know why - except that some systems seem to rely on sheer volume (all those extra mm’s mounting up) of product to hide everything.
Coating The Roof
This can be done by most people by hand, but it needs diligence and checking for correct film thickness.
Spraying is much faster but is a highly skilled job and the sprayer should not only be properly trained, but they should also really understand the equipment. Many jobs are delayed, and days lost because the person doesn’t understand their equipment or differences in coatings.
Spraying a thin, highly solvented or water-based paint is one thing, but spraying a 100% solid, solvent free high-performance coating is another. Not rocket science, but we have seen numerous simple avoidable mistakes that have caused delays and expense. These include:
- Having an underpowered pump
- Having a pump with too low a flow rate (flow rate can be more important than pressure)
- Having too small-bore hoses
- Using hoses that have been used for water-based coatings (cardinal sin that causes blockages as the old paint is stripped from the hose linings)
- Using an air-driven pump with too small a capacity compressor
- Wrong size tip
- Not setting up properly and getting the correct film thickness at the outset
- Poor spraying technique
Concluding Thoughts
Here are some concluding thoughts to drive home the importance of the applicators in the sealing process:
The application needs to be accurate and fast to keep a job on time and on budget, as per the sealant bead size example described above.You need to be able to rely on the applicator to make it accurate and for there to be no sign of a sheet edge in order to ensure longevity.
A mastic sealant with superior adhesive power will help and also prevents the lap ‘popping open’, which can happen with weak silicone.
So, next time you dismiss the contractors as ‘just the applicators’ think carefully about the crucial role they play in ensuring your project’s success, and how every millimetre counts towards a project that’s on-time, on-budget and done to a high-standard.
Further Reading
If you enjoyed this post, here are some further materials that you might find interesting:
3 Steps to Deal with Rust on RoofsMetal Roof Protection: What Are the Coating Technologies?
What Is the True Cost of Corrosion?